Manufacturing
The Manufacturing area includes transactions involved with the production of new materials or products. Minimally, manufacturing begins with the removal (adjustment) of items used (aka. raw materials) and ends with the result being some kind of "output" item or finished goods. In addition to the handling of both input and output items (raw materials and finished goods), manufacturing has a few other features. Adjustments are available so that expenses may be added into the cost of the manufactured item (such as labor, for example).*
In addition, manufacturing may optionally be assigned to a process. Processes can include pre-defined stages of manufacturing with an overall duration and a listing of default adjustments.
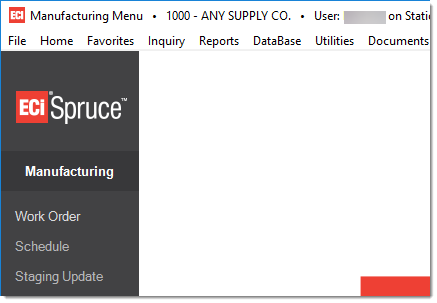
Manufacturing Menu
*Manufacturing adjustment codes must be defined prior to use. Only adjustment codes defined for use with manufacturing may be used (adjustment codes for Point of Sale and Purchasing cannot be used).
Getting Started
Manufacturing takes some planning. It's probably easiest to begin with one single manufacturing process to become familiar with the process works. A "manufactured type" item is required as the end product of the manufacturing process. This item is set up in the Item Maintenance form (Database menu) just like any other item; however, before doing this, there's some other setup to consider.
An optional feature for use with manufacturing is the "manufacturing process." Processes can be defined as a series of stages or steps. Each stage can have a selection of adjustments associated with it. The process, once defined, can be referenced from the Work Orders transaction.
A manufactured item may optionally be linked to a material list. The material list offers the ability to group together items, prompts, comments, and/or other material lists (which also may contain a mix of items, prompts, and comments). Material lists are useful because they can help organize and group the items and options used to manufacture an item. A material list should be defined before setting up the manufactured item if it is to be used. If material lists are not used, any items used for manufacturing will have to be entered each time manufacturing is done. Material lists can be added from the Material List drop down under Inventory.
Raw materials items can be entered during manufacturing or included in a material list (the material list may be linked to the manufactured item). The raw materials must exist in the item database.
Adjustment codes specific to manufacturing need to be added. These codes may be mapped to specific ledger accounts or the default mapping for manufacturing adjustments may be used instead.
Specific mapping exists for use with manufacturing. Users should minimally map the Inventory system journal for the 3 manufacturing accounts. Detailed mapping based upon product group for both raw materials and finished goods exists as well as mapping linked to manufacturing related adjustments (labor costs, etc.).
Work Order
This transaction is provided for specifying the materials and adjustments used for manufacturing as well as optionally tracking the stages of production.
Schedule
This transaction is provided for scheduling (assigning) and tracking manufacturing processes.
Staging Update
This area is limited to updating the stage of manufacturing for a given work order and item.