Physical Inventory Procedures
A Physical Inventory is done to obtain a more accurate valuation of inventory by correcting any discrepancies or mistakes that have occurred over time. Most businesses close and perform a full physical inventory at least once a year (usually this is timed near the end of the fiscal year). In addition, many businesses regularly count sections of inventory throughout the year (aka. "cycle counting") while open. Some choose to do just one, others do both.
In the application, physical inventory may involve three separate steps: initializing, counting, and posting.
Understanding the Physical Inventory Process
The purpose of a physical inventory is to make sure the total valuation of your company's inventory is as close as possible to the actual value. This valuation may be used for financial and tax reporting. Posting causes an adjustment to the dollar value of your asset inventory in the ledger. The total inventory adjustment will appear in the system Inventory Journal created by daily processing (scheduled between business days). If you post inventory several times over a period of days, the total adjustment will need to be calculated manually.
Important! If you are doing a full physical inventory near the end of the calendar or fiscal year for your company and you want the corrected value of the inventory to appear on inventory based reports run for that same time period, you must complete your physical inventory before the end of that period! Adjustments to the ledger may be moved using manual journals to the prior year if generated in the next year; however, inventory adjustments to on-hand are made based upon the current date only. If you post counts in the next year, that's where the adjusted inventory will be reflected on reports.
Please read the topic Historical Data and Reports for more information about reporting considerations.
Step 1: Initializing Counts
This is an optional step and does two things: (1) initialing removes any existing counts and adjustment quantities and (2) enables the application to track new adjustment quantities immediately.
Here are some quick facts about initializing:
•Initializing is always branch specific (occurs for the current branch only).
•Initializing will remove any previous counts entered, so it should always be done beforecounts are entered, never after!
•Initializing does NOT mean that items that were not counted will be set to zero on-hand automatically. This can be done, but involves additional steps.
•Initializing can be done for all inventory or just selected sections of inventory (group/section, keyword, location, and classification {class, department, and fine line codes}).
•Initializing can either include or exclude non-stocked items, re-numbered items (special orders), and/or resale items.
•Initializing immediately activates quantity tracking. If items are sold (or returned), adjusted, transferred, or received after initialization but before counts are taken, the posted count will wind up being wrong and adjusted incorrectly.
•Only initialized items that have been counted are eligible for posting. Items that were initialized but not counted won't be posted!
How to decide whether to initialize counts
This can depend upon procedures you have chosen and also the type of physical inventory you are performing. In any case, it's important to understand what "initializing" does first so that you can make an informed choice.
Tracking Adjustments
Once a physical inventory is initialized --or-- a count is entered for an item, all changes to the initialized item's on-hand value are tracked from that point until counts are posted. This adjustment quantity represents the net change in on-hand from any sales/returns, adjustments, transfers, and receipts occurring during this period of time and will be backed out of any physical counts once counts are posted.
Sales and receipts are always assumed to have occurred after any counting was completed. To maintain accuracy, it's very important to count goods before any movement of inventory is allowed. If counts are not initialized, adjustment quantities are not tracked until after a count has been entered for the item.
Paper Record vs. Electronic Counts
Are you planning on counting items using printed worksheets or are counts going to be entered into either via the application or a mobile device running the AnyWare software immediately during counting?
Why does this matter? If you are using worksheets, it means that the counts from the worksheets will need to be entered into the software after the counting has been completed. If you are entering counts immediately, there can be a lower chance of stock movement (sales/receipts) prior to the count being posted (finalized). This tends to be an issue in either case (worksheets or device) when cycle counting.
Timing can be important during a physical inventory. If you plan on opening your business before all counts are entered from the worksheets, you should initialize. Or, if you are cycle counting and there's a chance of stock movement after counting but prior to posting, initializing is a good idea. Initializing enables adjustment quantity tracking and will correct your posted counts by any activity after counting (sales and receipts specifically). Being open or allowing any movement of stock during actual "counting" is strongly discouraged!*
*Although initializing enables tracking of sales and receipts, it does not maintain a record of when each sale or receipt occurred in relation to when a particular product was counted. For this reason, it is always assumed that any movement of inventory occurred after a count was taken. If you initialize but count items after sales or receipts are processed for the items, the ending adjustment and on-hand quantities will be wrong. Companies should either close during a full physical inventory or count outside usual business hours... at night, for example. When cycle counting (limited areas), it obviously doesn't make sense to close your business, but the products being counted should be isolated from customer access, limited in scope (small sections), no receiving should be done, and the counts should be recorded and posted as soon as possible.
Are you using an Inventory Service Provider?
Hiring another company to count your inventory is convenient for some businesses. This avoids the cost of an interruption because most inventory services are able to count your stock outside of regular business hours. Typically, you would provide the inventory service a file containing a list of all of your inventory including item SKU's and UPC numbers minimally. After counting, the service would provide a file including either your item numbers (or the matching UPC numbers) and the counts taken.
Because there will be a delay between when the service counts your inventory and when they return the data to you, it's best to initialize all counts immediately before the service begins to count (after the close of business the same day, for example). This way any sales or receipts done after they count can be considered and adjusted once the data is returned, imported into the application, and posted. (Adjustment tracking enabled by the initialize step will automatically correct the on-hand adjustments, this does not have to be done manually).
Full Physical Inventory vs. Cycle Counts
When doing a full physical inventory, initializing is done for either (or both) of 2 reasons: (1) it's done because your company will be open after counts are taken during the time counts are being entered {from worksheets, etc.} --or-- (2) it's done because you want to set the on-hand values on items you did not count to zero. With regard to reason #2, initializing alone does not set on-hand values to zero for uncounted inventory, but it does make it possible to differentiate between the items that were counted and those that weren't.
When cycle counting, initialization can be less beneficial. This is especially true if you are unable to isolate the inventory from activity during counting (being open for business, for example). Initializing during cycle counting should only be done if you plan on posting the counts immediately after counting concludes and are able to control access to the inventory (stock movement) during the time the stock is being counted.
Initializing cannot be done by item, so unless the goods being counted have something in common in the data, you may not be able to initialize them without also affecting other products. For example, if I wanted to count the items in my "paint" department but those items are not assigned any location code and don't have some other similarity in the data (same group/section, etc.), initializing just those items may not be possible. The Count Variance report can be used to get a listing of items that haven't been counted in the last 30 days, this can be used to check uncounted inventory (as a substitute for initializing).
At what time should counts be initialized?
For a full physical inventory, this step should be done after the close of business andbefore any counting is done. No changes to on-hand should be permitted between initializing and the completion (recording) of all counts. Count entry can be done while open; however, the count itself is always assumed to have occurred prior to any sales, receipts, or other changes to on-hand quantities for items.
For a limited cycle count, you need to be careful. If done, initialize immediately prior to counting and only initialize the section of inventory being counted (by location, for example). If the area being counted cannot be initialized by itself, it's usually best not to initialize. The count area should be limited in scope. Access to the count area by customers should be restricted until all counts are taken (if a customer does need to buy something that hasn't been counted, either count the item before the customer takes it or make sure the quantity the customer took is included in the count quantity for the item).
What if I want uncounted items to be zeroed?
If it is your intention to clear items that are not counted to zero on-hand, this is not done automatically. To set uncounted items to zero on-hand requires that counts of zero be entered. There are shortcuts available for doing this from the Enter Counts area in Inventory prior to or after counting.
Where do I initialize counts?
To initialize your physical inventory counts, from the Main Menu choose Inventory > Utilities > Updates > Initialize Physical Counts.
The Initialize Counts form is available from the Utilities drop down menu in the Inventory area (see below).
Step 2: Entering Counts
This step is the process of recording physical counts for items. Once a count is entered for an item, the adjustment quantity cell is enabled and will track any changes to on-hand from sales or inventory receipts. Before posting, all counts are cumulative, so if more than one count is entered prior to posting, they will be added together. Negative or positive counts can be entered to fix mistakes with a prior counts when necessary (as long as it's prior to posting, after posting, it's necessary to enter a total count for the item and re-post).
Methods
There are several possible ways to enter counts:
•Items being counted can be scanned or entered directly into the application's Physical Counts area. To make this feasible, consider using a wireless network and lap-tops or a PC on a cart with either a wireless or cabled network connection.
•The optional AnyWare app can be used to collect physical counts on an Android™ platform device.
•Counts can be entered based upon manually counts recorded on paper (count worksheets), for example. A standard report, Count Worksheet, exists for this purpose. Use the Import (F2), Worksheet option to import items from a previously saved worksheet (report settings must have been saved for this option to be used). If the worksheet settings are not saved, choose an option similar to how the report was generated (location, group/section, etc.).
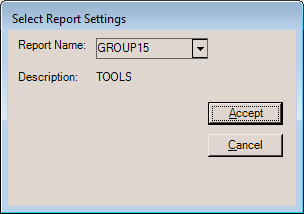
Import (F2), Worksheet
•Counts can be imported from a Windows-based file such as a spreadsheet. If using an inventory service for counting, this would be used to import the service's data into the software for updating. Choose Import (F2) and Wizard to import items from a spreadsheet.
•Inventory can be imported (Import (F2) and Inventory) into the Physical Counts area by group (or group/section), keyword, location, or classification (department, fine line, etc). After import, users can enter counts for matching items in column-style entry. This might be used to match with a report using the same ordering.
•Uncounted initialized items can be copied into the Physical Counts area using the Import (F2) function.
Using the Physical Counts Form
Like most areas in the application, the Physical Counts transaction includes a few basic form fields (name and location) with an item grid. These are required and provide information that appears on the count session report.
Until posting, all counts recorded for the same item are cumulative (even if the counts are recorded at different times by different users). A new count never replaces any "previous" count appearing in the Physical Counts grid.
Entering Counts using a Different Unit of Measure
It's possible to enter a counted quantity using any of an item's unit of measures; however, it's important to understand that ALL quantities shown in the Physical Counts grid match the item's BASE unit only. Although it's possible to enter the count quantity using a different unit of measure, the quantity entered is immediately and automatically converted back into BASE U/M terms.
Warning Signs
If you see a quantity in the "Sold/Recv" column when entering counts, it can indicate a problem in some cases. During actual counting, this should show a zero. If the figure is not a zero, it means that the item's on-hand has changed due to sales, returns, quantity adjustments, transfers, or receiving either (1) since the item was initialized or (2) since a prior count had been entered. This may be OK if you counted while closed but are open while the counts are entered into the software or if you are counting an additional quantity that wouldn't have been affected by the stock movement of the item. It indicates a problem if you haven't yet saved any count for the item. Sales, returns, receipts, or other changes to on-hand quantities prior to completing the counting process can cause ending adjustments to be wrong.
Using Physical Count Entry for Review*
There are several functions built into the Physical Counts activity that are useful for reviewing counts prior to posting. Before beginning, populate the grid with items (use the Import (F2) function and choose Inventory to do this, for example). Copy in all or a portion of your inventory that had been counted using the options provided (if you have a large inventory, it's best to split this up). Once the grid has been populated with items, you can use the Style (F3) function to choose Variance Display. This will change the grid's appearance. The last column in the grid will be "App Cost Adj" (applied cost adjustment). Click on this column to sort the items from highest cost adjustment to lowest and also the reverse. Carefully check to see if any item's cost adjustment amounts are unusually large. Often, these indicate an error counting. Fix any errors and check again.
*Note: the Count Variance report available from the Inventory area, Reports menu can be used for this purpose as well.
Negative On-hand Items
Since an item cannot legitimately have a negative on-hand or value, it makes sense to set the count on any negative on-hand items to zero. This can be done prior to counting, during counting, or after counting. Use the menu marker in Physical Counts entry to do this after items have been copied into the grid (possibly after using the Import (F2), All Uncounted option).
Step 3: Posting Counts
Posting is the last step which completes the physical inventory process and is the only step that adjusts on-hand quantities. The action of posting affects just those items that were counted.
To determine the quantity to adjust (if any), the software adds the counted quantity and the adjustment quantity (if any).* The adjustment quantity represents any changes to the on-hand since counting or initializing. If the total (sum) of these 2 figures does not match the item's current on-hand, the item's on-hand is adjusted to match the total. Otherwise, if the total of the count and adjustment quantity matches the item's current on-hand, no adjustment is necessary. Posting also updates the last count date for the counted items.
*The adjustment quantity is a net total. It will be a positive figure in cases where there is an increase in on-hand, negative when there's been a net decrease, and zero if there is either (1) no activity from sales or receipts or (2) all stock movement activity nets to a zero total. Sales, Returns, Quantity Adjustments, Transfers, and Receipts affect the adjustment quantity.
Prior to Posting
Due to the nature of counting inventory, there's plenty of room for human error. It's strongly suggested that someone review counted quantities prior to posting to catch any large errors (entering an item number or barcode as a count is one common accident). We suggest using the Count Variance report for this purpose.
Counts are cumulative, so they can be corrected by entering either another count (positive or negative) to fix any errors you locate. Remember, the adjusted value of inventory is typically used for tax reporting and financial statements, so if the figure is off by a substantial amount due to counting errors it's a very good idea to find and correct it early!
How to Post
Just as with Initializing, Posting is available as a Utility function. From the Inventory area, choose the Utilities > Updates > Post Physical Counts. The same options available for initializing are available with posting.
Only items that have had a count entered are posted. Any items that were initialized but not counted remain in the process of inventory until a count is entered and posted. Users can choose to enter zero counts for any uncounted inventory that was initialized or set the counted quantities to match the item's existing on-hands. Posting won't clear or otherwise change the status on an "initialized" item that hasn't been counted.