Handling Item Returns
Realizing that all returns are not handled the same way and to better assist our users, we have enhanced the way item returns are handled by the software. If the enhanced "Stocked Item Returns" option is enabled, you will have a choice whenever any item is returned to either restock or create a vendor return. In this case, vendor returns generate a document for each returned item that is not a "restock."
When a customer returns an item, there are a number of things to consider:
•Condition of the Product
Products may be returned for a number of reasons and in some cases can be resold to another customer; however, they also may be damaged, used, or have missing/damaged packaging, etc. The condition of the return may affect whether or not your company chooses to accept the return for either refund or exchange. In addition, should you accept a return, the product's condition may be a factor in what you do with the item afterwards (attempt to resell(restock), return to the vendor, sell to an auction, donate, discount, or dispose of).
•Is the product eligible for return?
You can designate that any particular item not allow returns. This is commonly used for special orders (non-stocked items) and products that involve customized changes such as custom mixed paint colors, food items, and any products that are cut to a specific size for the customer (glass, screen, carpet, rope, chain, moulding, etc.). You can assign a message code that prints on Point of Sale documents to state that returns are not accepted (or post a sign, etc.).
•Did your company sell the item to the customer?
Unfortunately, it's common for shoplifters to attempt to return stolen merchandise for refunds or exchange. For this reason, it's a good idea to validate the return against your sales (invoice) history. If the customer doesn't have a receipt, ask for the purchase date, the payment method, and any other information to validate the purchase. Ask for identification and record the customer's information in the Process (F12) form. Some companies only refund money using Payables checks after validating the return. Most shoplifters won't want to wait or return in a few days for a check.
Even if the customer has a receipt, make sure that there aren't any prior returns against the same document and item. And, if there's any question, make sure that the current on-hand for the item is accurate. If the on-hand doesn't match the shelf quantity, you may have a theft issue, but not necessarily. Whenever a customer returns merchandise, either keep their receipt or mark it so that it's clear that it was previously used for a return (this can prevent someone from using the same receipt for multiple returns of the same item).
After you accept the return of an item, you also must decide how to handle it.
-
Items may be restocked if they are in suitable condition for resale.
-
You may return an item to a vendor or manufacturer for credit or replacement. Products you purchase from a hardware co-op or wholesaler typically are assigned some type of return policy. This policy may allow you to claim a credit without having to physically return the item in certain cases.
The return process for non-stocked products hasn't changed much; however, there is a special form for stocked items that are being returned.
Pro Tip: When a customer returns more than one product and they were purchased on different invoices, we recommend you process the returned items pertaining to the same original invoice together but items on different invoices on separate transactions. This is particularly important for accounts that process invoices with terms discounts. Not doing so tends to affect the discounts in unexpected/unpredictable ways.
IMPORTANT: For invoices with terms, the discount on those invoices can be reduced if returns are processed referencing the invoice later. Check the document links for the terms invoice to see any returns linked with the sale if you notice or are questioned as to why a discount was reduced.
How do I enable Enhanced Item Returns?
There are 2 parameters that enable enhanced returns tracking. One parameter is used for stocked items, the other for non-stocked items. This allows you to use the enhanced returns feature with either, neither, or both types of items at your discretion. These parameters are located in the "Settings" tab located on the Point of Sale tab of the Parameters form (access this from the Database drop down menu in the Maintenance area). User security permissions can limit access to this area.
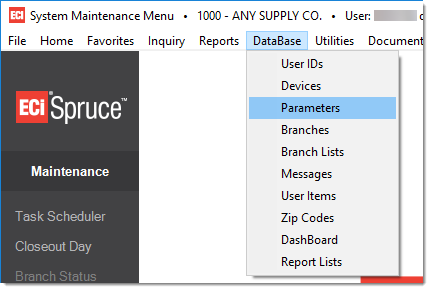
For more information about these parameters please click here.
Excluded Items
The enhanced returns feature does not apply to all item types. The following item types do not create returns:
•Deposit Items
•Hardwoods Items
•Gift Card Items
•Rental Items
•Material List Items
•Tally Items
*Any specific item may be set to not allow returns. If this is the case, a message is produced at Point of Sale and the Item Return form is not provided.
Handling Stocked Item Returns (when the Stocked Item Returns Parameter is Enabled)
When the enhanced stocked item returns" parameter is enabled, you can choose to restock or create a vendor return when a customer returns an item. In this case, returns generate a document for each returned item that is not a "restock." The "Item Return" form appears when returning an item. This allows the Point of Sale user to specify the original sale invoice, reason for the return, whether the return is a "restock," and to optionally add a more detailed note regarding the reason the item is being returned. If you are creating a customer order rather than a sale or charge return, this information will be saved along with the item until the order is invoiced (completing the return).
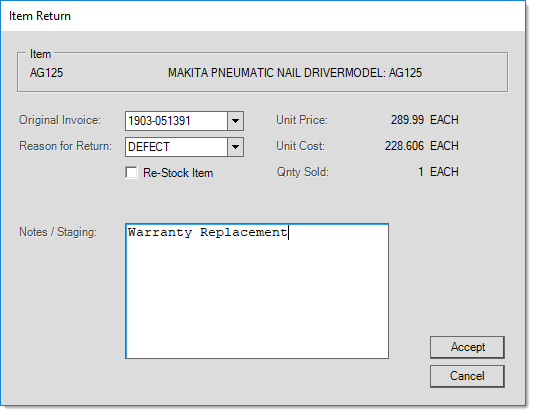
Item Return for Stocked Item
Original Sale Invoice
This is a list of this account's invoices that contain this item. The selection listing includes the Document ID, transaction date, account, job, name, and invoice total.
Unit Price
This is the unit price from the selected "Original Sale Invoice." The price of the return will be set to equal this price if an original sale invoice is designated.
Unit Cost
This is the unit cost from the selected "Original Sale Invoice." This cost will be used as the cost of the item for the return.
Return Reason
This is a drop down containing preset selections for return reasons. Your company determines the selections (these are defined in the Code Maintenance form's "Returns" tab -- available from the Inventory area's Database menu). If your company has not yet or chooses not to populate preset return reasons, reason selection is not required. Users can type their own reason in the drop down text area as well (space is limited to 10-characters, however).
Restock
This check box determines whether to immediately return the item to inventory (increase the on-hand) or to instead generate a vendor return for the item. If the Restock check box is selected (checked), no vendor return document is created.
Note: the vendor return may be designated for restock by later processing.
Notes/Staging
If needed, add more details about the return. These are saved in the same way staging notes are saved with items may be printed on the return document.
Non-stocked Item Returns
When returning non-stocked items during a Point of Sale transaction, users are presented with a form similar to the one used when ordering non-stocked products. The appearance of this form may vary based upon the return options your company has selected for non-stocked products. When the enhanced non-stocked returns option is enabled (via a Point of Sale parameter), a "re-stock?" check box is provided allowing you to either (1) immediately return the product to inventory or (2) create a vendor return. Creating a "vendor return" does not adjust the item's on-hand and adds the item to a database table for further processing (the item can still be designated for resale (restock) at that time). When the enhanced vendor returns option is not enabled, no "restock" option appears and the item's on-hand is always updated (there is no vendor return document created in this case).
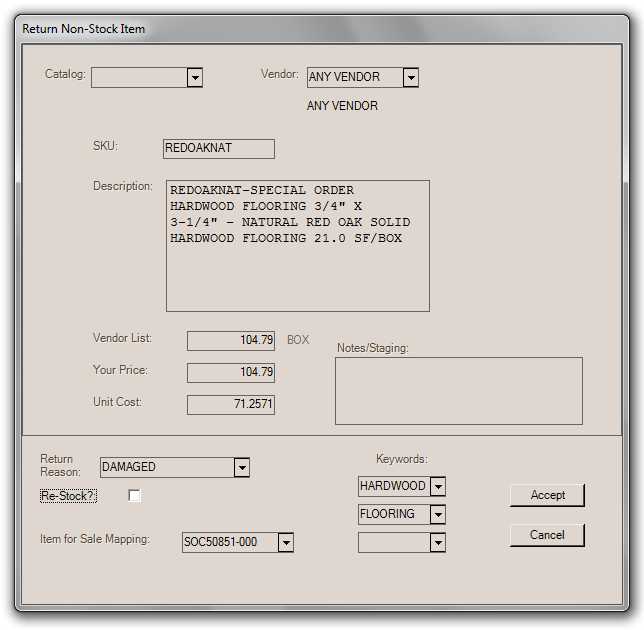
Return Non-Stock Item: Enhanced
The form will populate with varying amounts of information based upon the status of the item at the time of return. Non-stocked items typically follow a work flow similar to the following:
•A customer places an order for the item. A customer order document is created from Point of Sale.
At this stage, a generic non-stocked SKU is typically used. When the customer order is processed, a unique "renumbered" SKU is created. This item's committed quantity is increased. If a purchase order was created from Point of Sale, the on-order quantity is also increased.
•A purchase order is sent to the vendor for the item.
•The vendor ships the item and it is received into inventory.
As soon as the item is received, the item's type is changed from "renumbered" to "resale." On-hand is increased by the receipt and any on-order quantity is reduced.
•The ordered item is invoiced in Point of Sale.
The resale item's on-hand is reduced by the sale.
•The customer returns the item.
Minimally, the form will populate with a description, vendor list, unit (your) price, unit cost, and any keywords associated with the item. In some cases, the form may automatically set the vendor, vendor SKU (usually this is also in the item description when the order was placed by selecting a catalog item), and notes/staging; however, this is only done for renumbered type items. The vendor information can be specified later for vendor returns and isn't necessary if you are restocking the item.
To process the return, choose a return reason, select re-stock if the item is being returned to stock immediately, and enter any notes (in the notes/staging text area). Click the Accept button to complete the return information and Process (F12) the return sale.
What happens to an item and to the ledger when the item is returned?
If the enhanced returns is not being used, the following happens when any return is processed:
•The item's on-hand is increased by the quantity returned immediately.
•The item's usage for the current month is reduced bye the quantity returned immediately.
•The item's sales and cost totals are affected for the month immediately.
•That business day, your company's ledger (G/L) asset inventory is increased by the extended cost of the returned item.*
•That business day, your company's ledger (G/L) Cost of Goods sold account is decreased by the extended cost of the returned item.*
*Daily (End of Day or EOD) processing creates journal entries.
When enhanced returns IS enabled and you are not immediately restocking the item, the above actions still occur except for the item's on-hand adjustment.
•The item's on-hand is only increased if the item is later designated for either restock or resale.
•In the case of resale with stocked items, a new unique tracking item is created. Only the new item's on-hand is adjusted, not the original item's.
•When items are marked for resale (not as a vendor credit), an adjustment to the ledger is not necessary because the asset inventory value was previously increased on the day of the return.
•No on-hand adjustments are made when an item is being discarded or returned to the vendor.
•Because asset inventory and cost of goods are affected whenever an item is returned, it becomes necessary to adjust asset inventory if an item is being discarded (it is being removed from your inventory). Users are asked to specify the ledger account offset to the inventory adjustment in these cases. This adjustment occurs when the vendor return status is updated to one of the discard types, this may be not the same day or ledger cycle as the original return necessarily.
•In the case of an item that's being returned to the vendor, an inventory receipt is created that generates a ledger entry reducing your asset inventory (credit) and lowering the balance in the accrual account (debit). Processing the Payables credit invoice then credits the accrual account (increasing the balance) in order to move it's balance to your accounts payable account (a debit that decreases the liability balance). The payment of the credit increases the Accounts Payable balance and reduces the cash paid out to the vendor (this assumes the credit is applied toward a payment to the vendor... reducing the amount paid).*
*If you don't transfer your payables invoices prior to payment, the purchase/expense and payment entries are done at the same time.
Vendor Returns Processing
Any items a that are not immediately restocked create a vendor returns document and the vendor return may be processed further from the Item Returns Utility available from the Inventory area. This area allows you to decide upon an "action" to apply to the returned item.
These actions include the following:
None
✓No immediate action taken.
Return to Stock
✓Adjusts On-hand for the Item.
✓No G/L Adjustment is needed.
✓Vendor Return document is closed.
Return to Resale
Stocked Items
✓Creates a separate and unique tracking SKU for the Item.
✓Creates a closed credit inventory receipt for the item. No ledger (G/L) adjustment.
✓Adjusts the new item's Quantity On-hand.
✓Closes the Vendor Return document.
Non-stocked Items
✓Forces the status of the item to "resale" if it's not already.
✓Adjusts the item's Quantity On-hand (without any General Ledger adjustment).
✓Closes the Vendor Return document.
Vendor Credit - Discard Processing
✓Creates a credit inventory receipt for the item.
✓An inventory journal is created for the day the vendor return is processed as "vendor credit - discard." This reduces the asset inventory value by the extended cost of the item and decreases the accrual account by the same amount.
✓No adjustment to the item's On-hand is necessary.
✓Closes the Vendor Return document.
Vendor Credit - Resale Processing
Stocked Items
✓Requests an adjustment type during vendor return processing.
✓Creates a separate and unique tracking SKU for the Item.
✓Creates a credit inventory receipt for the item.
✓An inventory journal is created for the day the vendor return is processed as "vendor credit - resale." This reduces the asset inventory value by the extended cost of the item and decreases the accrual account by the same amount.
✓Adjusts the new item's Quantity On-hand.
✓Creates an inventory adjustment using the adjustment type selected to add the new item to inventory.
✓Closes the Vendor Return document.
Non-stocked Items
✓Requests an adjustment type during vendor return processing.
✓Creates a credit inventory receipt for the item.
✓An inventory journal is created for the day the vendor return is processed as "vendor credit - resale." This reduces the asset inventory value by the extended cost of the item and decreases the accrual account by the same amount.
✓Adjusts the item's Quantity On-hand.
✓Creates an inventory adjustment using the adjustment type selected to re-add the item to inventory.
✓Closes the Vendor Return document.
Return to Vendor Processing
✓Creates a credit inventory receipt for the item.
✓An inventory journal is created for the day the vendor return is processed as "return to vendor." This reduces the asset inventory value by the extended cost of the item and decreases the accrual account by the same amount.
✓Closes the Vendor Return document.
Discard - No Credit Processing
✓Requests an adjustment type during vendor return processing.
✓Adjusts the item's Quantity On-hand without affecting G/L (asset inventory currently reflects the item's value).
✓Creates an inventory adjustment using the adjustment type selected to remove the item from inventory (and adjust/reduce the item's on-hand)
✓Closes the Vendor Return document.
For more information, please see the help topic on the Item Returns Utility.