Manufactured Non-Stock Item
In Point of Sale, when a non-stocked manufactured item is linked with a customer order, a special form opens. At this time, users can specify a price and cost or just a markup percentage for determining the amount later. A deposit may be linked to the item or the customer order. The "Added to Work Order #" label will show the manufacturing work order ID only after the customer order has been copied into the manufacturing area and saved.
Manufactured items that are non-stocked may optionally be associated with a material list. The form presented at Point of Sale is a bit different depending upon whether the item is assigned to a material list or not. If no material list is associated, the form is much simpler; however, when a material list is associated with the non-stocked manufactured item, selections can be made during ordering (see below).
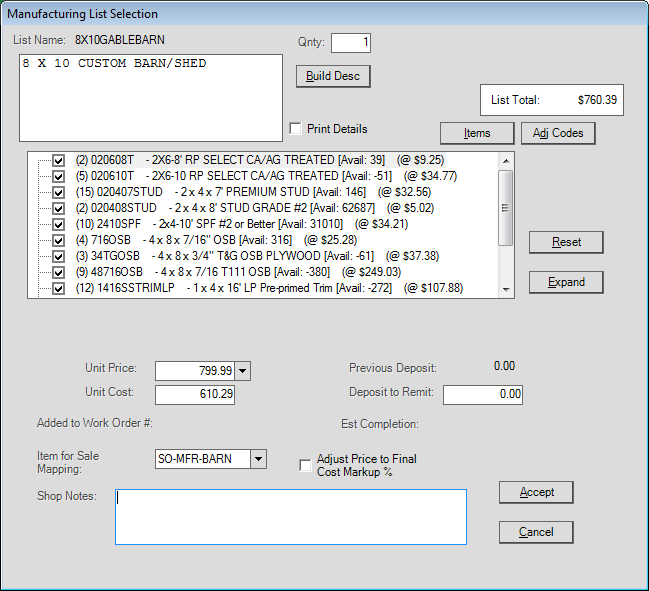
Manufacturing List Selection
Manufactured non-stocked items function similar to other non-stocked items. Each non-stocked manufactured item will be assigned a unique stock number for tracking purposes. The item code format for manufactured goods is prefixed with the letters "MN" followed by the order number and a 3-digit sequence number (based on the number of manufactured items on the customer order). This unique item number is created when the order is processed (see the example below).
MNC12345-001 ("MN" + Order Number + "-" + Sequence)
Here are some descriptions of the fields and options available during ordering from Point of Sale:
Qty (Quantity)
For cases where more than one of a particular manufactured item is being requested, a quantity field is provided. The quantity can also be changed from the data grid when ordering.
Build Desc
This button creates a detailed description based upon the selections made in the materials tree. The "Build Desc" button only appears if the manufactured item has an associated material list. The description only updates when the button is clicked. Changes made to material list options are only reflected if you click the "Build Desc" button after making changes. Any manual changes made to the description, if allowed, are overwritten each time the "Build Desc" button is used.
Items or Lists (Button)
This button toggles the display and allows you to enter additional items to be associated with manufacturing (such as add-on or replacement items that aren't included in the material list selections). When selected, the material list or adjustments panel is temporarily hidden from view and a grid appears where items may be listed. The button text is changed to "Lists" while the item entry grid is displayed. This option is only provided for non-stocked manufactured items that have an associated material list.
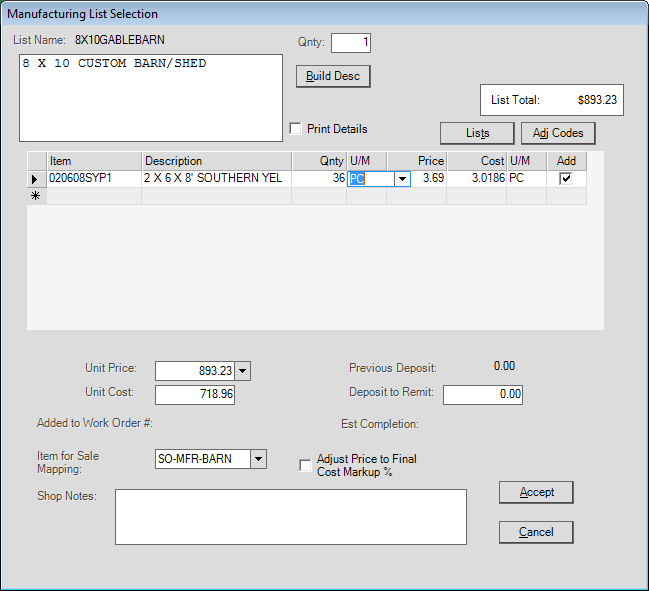
Manufacturing List Selection (Items)
Adj Codes (Adjustments) or Lists (Button)
This button allows the user to specify adjustments along with the items and list selections (if any). Adjustments provide a way of better estimating the cost of manufacturing especially when the price is being based on the overall cost of materials and those adjustments. If the button to the left of "Adj Codes" shows the text "Items" at the time it is clicked, the text of the "Adj Codes" button will change to "Lists" once the adjustments panel and data grid are displayed. If the text of this button (left) is set to "Lists" when the user clicks the "Adj Codes," it will be reset to "Items" and the current button (right) will now change to "Lists" instead.
Lists (Panel) |
The "lists" panel is displayed after clicking the "Lists" button (which may be either the left-hand or right-hand buttons displayed below the "total" panel.
Reset This button is provided along with the material list selection panel. If clicked, the material list selections are changed back to their original default values and any changes or entries made by the user are undone. This option is only provided for non-stocked manufactured items that have an associated material list Expand The "expand" button maximizes the selection tree so that all nodes (items, descriptions, etc.) are visible (expanded) for each level (users may still need to use the scroll bar to view all the expanded options). This option is only provided for non-stocked manufactured items that have an associated material list. In some cases, a material list include prompts that require some type of response by the user. When prompts are included and selected in the list "tree," the prompt and an input area for your answer are provided below the "list" panel.
Additionally, selected item levels may require that a quantity be entered if no default quantity was indicated for the item. |
Unit Price
This is the unit price for the entire manufactured item. The price may be either based on any added items, adjustments, and material list selections (meaning changing selections affects the price) or it may be a set price that doesn't change when selections are changed.
Unit Cost
Unit price is an estimated cost based upon the material list selections, adjustment costs (if any), and any additional items specified. This cost will likely change since costs may change between now and when the item is manufactured (not to mention any expenses/adjustments added during the manufacturing process).
Adjust Price to Final Cost Markup %
If a markup percentage is specified for the item's price, and this option is selected, the unit price will be calculated as a markup percentage using the cost of the manufactured item including materials and adjustments at time of sale. This cost and resulting price won't be final until after manufacturing has completed. If not selected, the final price won't be adjusted if the costs or adjustments change during manufacturing.
Added to Work Order #
If the non-stocked manufactured item has already been associated with a work order (meaning, the customer order has begun processing in the Inventory, Manufacturing area), the document identifier will be displayed here.
Previous Deposit
If a deposit was previously associated with this non-stocked manufactured item on this order, this will display the amount of deposit linked with this item. No previous deposit amount will appear during initial order creation.
Deposit to Remit
Use this field if you are adding additional deposit to the non-stocked manufactured item. Deposits may also be associated with the customer order document overall instead of by specific items.
Estimated Completion
Once a customer order with non-stocked manufactured items has been associated with a work order in Manufacturing, an expected completion date is assigned and will be displayed here in this case. This field will not display a date during initial order creation.
Item for Sale Mapping
This field defaults to the original non-stocked manufacturing SKU used for ordering this manufactured item. Once the customer order is processed, a unique tracking SKU is created for the item. Eventually, once all activity on the generated item is completed, the sales and usage information will be merged back to the original item.
Shop Notes
This area is provided for shop notes (special instructions for manufacturing). These notes appear on the Entry folder tab in Manufacturing along with an icon on the tab to designate that additional information is present. Shop notes do not appear in Point of Sale folders.
Accept
This button is used to accept any changes and close the non-stocked manufactured order entry form. To re-open the form, click on the item's description.
Cancel
This button closes the non-stocked manufactured item form without saving any changes made to the item.
Other Information
Here are a few points regarding Manufactured items containing non-stocked goods:
•The items associated with the material list may be stocked, non-stocked, or both. Non-stocked items require a description, quantity, and price when selected or required.
•If no material list is associated with the non-stocked manufactured item, the form used is similar to the standard non-stocked order form.
•Purchasing information regarding the special order elements in the material list are specified in the Manufacturing area, not Point of Sale. A purchase order can be assigned or created in manufacturing for any special order goods required.